Guidages en rotation par roulements
Transmettre les efforts - Durée de vie (Choix des dimensions)
III-A: La fatigue
Mécanisme de l'ECAILLAGES DE FATIGUE
En fonctionnement normal sous charge, les surfaces actives d'un roulement sont soumises à des contraintes alternées très élevées dues aux passages successifs des corps roulants sur les chemins. Les contraintes de compression peuvent atteindre 3 500 N/mm2 et les contraintes de cisaillement 1000 N/mm2. Elles finissent par créer, à plus ou moins long terme, des fissurations par fatigue de la matière.
Ces fissures naissent en général en sous-couche et se propagent vers la surface. Elles provoquent alors le détachement d'écailles d'acier - phénomène qu'on appellera l'écaillage. Le chemin de roulement se trouve alors endommagé, le roulement perd rapidement ses propriétés initiales, et n'est donc plus en mesure d'assurer son service.
L'écaillage s'explique par l'imperfection de la structure de l'acier qui contient toujours des micro-inclusions, lesquelles facilitent, à plus ou moins long terme, l'initialisation de la fissuration. Même s'il est difficile de les détecter en laboratoire, Ces inclusions existent. Le roulement aura une résistance à la fatigue d'autant plus grande que l'acier qui le compose sera fin et homogène - c'est-à-dire que les micro-inclusions seront petites et dispersées.
|
|
La détérioration par fatigue d'un roulement en fonctionnement dans des conditions normales de charge, vitesse, température et désalignement est un phénomène normal et inéluctable. Pour mieux apprécier ce phénomène, on peut procéder par analogie avec une route asphaltée: le revêtement est conçu pour supporter des conditions sévères de circulation; pourtant, à l'intérieur de l'asphalte, peuvent s'être immiscées des «impuretés » (cailloux), qui, au bout d'un certain nombre de millions de compressions cycliques, dues aux passages des véhicules, vont fragiliser le revêtement et amorcer un petit nid-de-poule. Celui-ci ne cessera de s'agrandir après le passage de plusieurs véhicules, et conduira enfin à poser des problèmes aux dits véhicules; dans ce cas, la route ne sera plus praticable.
Le problème posé par ce phénomène de fatigue est son aspect aléatoire, qui en rend l'étude difficile. En effet, des roulements identiques, fabriqués à partir d'un même lot de matière, ayant des caractéristiques géométriques identiques, soumis à des conditions de fonctionnement identiques (charges, vitesse, lubrification) se détériorent après des durées de fonctionnement très différentes (il en va de même pour l'état des routes). Cet aspect étant connu, il s'agit donc d'établir la probabilité de fatigue d'un lot de roulements. Cette étude est celle d'un phénomène aléatoire: la durée de vie n est pas une donnée de précision, mais une notion statistique.
|
|
III-B: Essai de référence
Etude statistique: Prenons un lot de cent roulements identiques , et faisons les tourner sous une même charge radiale P1 jusqu'à mise hors d'usage par fatigue.
Si nous représentons, en fonction du nombre de révolutions accomplies, le nombre de roulements en état de marche, nous obtenons le diagramme de la figure 1.
On constate la très grande disparité des valeurs de durée de vie obtenues.
En général, le premier roulement est mis hors d'usage assez rapidement, alors que la moyenne des durées de vie obtenues (valeur atteinte par 40% des roulements) correspond à une durée 5 fois plus longue, et que le dernier roulement atteint un nombre de tours environ 20 fois plus important.
Des essais effectués avec des vitesses de rotation différentes montrent que celle-ci n'a pratiquement pas d'influence sur la durée de vie et que seul compte le nombre de révolutions réalisées.
|
|
Influence de la charge appliquées: Recommençons la même expérience, toujours avec les mêmes roulements, mais avec des charges Pi différentes.
Nous obtenons des durées de vie moyennes fonctions de ces charges. L'allure de variation de cette fonction est donnée par le diagramme ci contre (Fig. 2).
Si nous représentons maintenant en coordonnées logarithmiques, le nombre de révolutions atteint en fonction de la charge appliquée, le diagramme prend alors l'allure ci-contre (Fig. 3). Nous constatons que les points caractéristiques s'alignent sur une droite.
|
|
En représentant maintenant, toujours en coordonnées logarithmiques, le nombre de révolutions atteint par un certain pourcentage de roulements (par ex. 50 ou 90 %) sous une charge donnée, en fonction de
cette charge, nous obtenons alors le diagramme de la figure 4.
Les points correspondant à des pourcentages de tenue identiques s'alignent sur des droites parallèles.
|
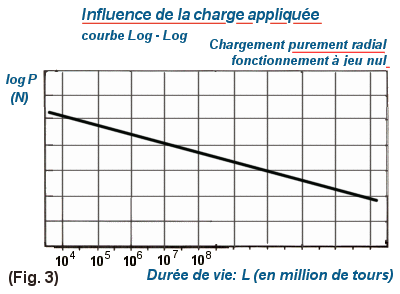
|
Définitions
La durée de vie en fatigue d'un roulement est limitée conventionnellement par l'apparition des premières traces visibles de fatigue (moment où la première petite fissure atteint généralement la surface du chemin de roulement de la bague intérieure).
On appelle DUREE DE VIE NOMINALE AVANT FATIGUE, et on note "L10" le nombre de révolutions, exprimé en millions de tours, atteint pour une charge donnée P, par 90% des roulements.
Le choix arbitraire , comme reférence de calcul, d'une survie de 90% des roulements, plutôt que de la durée de vie moyenne, a été fait par les constructeurs et normalisé par l'I.S.O., pour des raisons de sécurité.
On appelle "C", CAPACITE DE CHARGE DYNAMIQUE (ou taux de charge dynamique) d'un roulement, la charge sous laquelle au moins 90 % des roulements atteignent une durée de vie de 106 révolutions.
Remarque Entre le moment ou apparait la première fissuration sur un roulement, et celui ou de grosses écailles commencent à se détacher l'empéchant complètement de jouer son rôle de guidage, il peut encore effectuer un nombre de tours égal au dixième de la durée de vie nominale. Par contre, arrivé à ce stade, la destruction totale est très rapide et peut être néfaste à toute la machine.
Détermination de la durée de vie nominale L
Considérons la droite représentative de la durée de vie de 90% des roulements.
On constate que la pente de cette droite est:
- dans le cas de roulements à billes,
de -1/3 (contact ponctuels)
- dans le cas de roulements à rouleaux,
de -3/10 (contacts linéïques)
Ecrivons l'équation de cette droite entre les points A et B (dans le cas des roulements à billes):
Log P - Log C = - 1/3 (Log N - Log(106))
3.Log (C/P) = Log (N/106)
L= (C/P)3 (pour les roulements à billes).
De même,
L= (C/P)10/3 (pour les roulements à billes).
|
.gif)
|
Détermination de la capacité de charge dynamique minimale pour obtenir une durée de vie nominale L sous une charge constante P
Calcul de la durée de vie nominale en heures Lh
Soit "n" la vitesse de rotation exprimée en tours/mn
Capacité de charge statique d'un roulement
Dans le cas d'une durée de vie très faible (vitesse de rotation très lente ou roulement soumis seulement à des oscillations) le calcul de la capacité de charge dynamique nécessaire peut conduire à un roulement incapable de supporter la charge P qui lui est appliquée.
Celle-ci peut en effet causer, à l'arrèt des empreintes des elements roulants dans les chemins de roulements. On dépasse alors localement la pression de contact admissible (4600 Mpa). Ces deformations peuvent etre nuisibles au rôle de guidage du roulement, et peuvent amener une fatigue prématurée consecutive aux chocs occasionnés par le passage des elements roulants dans les empreintes.
On est donc amené à limiter la charge P que peut supporter dynamiquement un roulement, par une valeur Po, fonction de la géométrie interne du roulement et de la qualité de guidage que l'on veut assurer.
|
|
On appelle CAPACITE DE CHARGE STATIQUE et on note Co, la charge qui, appliquée sur un roulement, provoque aux points de contacts de l'élément roulant le plus chargé, une déformation permanente dont la dimension est égale à 1/10000 e du diamètre de l'élément roulant.
Cette définition est complétée par la suivante :
La charge statique de base est définie comme la charge radiale qui crée au niveau du contact (corps roulant et chemin) le plus chargé une pression de Hertz de:
4200 MPa pour les roulements à billes.
4600 MPA pour les roulements à rotules sur billes.
4000 MPa pour les roulements à rouleaux.
Détermination de la charge statique maximale PO admise par un roulement de capacité de charge statique C0.
On utilise l'équation: Po = Fs.Co
avec Fs coefficient de charge statique qui tient compte de la déformation locale admise en fonction de la precision de guidage et de la douceur de fonctionnement exigées.
- pour des exigences normales on choisira Fs voisin ou egal à 1.
- pour une grande precision Po doit être diminué, Fs peut être ramené à 0.8 , 0.6 voire 0.4.
- pour un fonctionnement quelconque Fs peut etre supérieur à 1, et peut prendre des valeurs de 1,2 jusqu'a 2.
Remarques:
- Dans le cas d'un montage dans un logement a paroi mince, (risque de de formation globale de la bague exterieure ) il faut diminuer la valeur de Fs.
- les butées à rotule sur rouleaux exigent pour un fonctionnement correct, une valeur de Fs<0,5
III-C: Passage aux chargements réels
Soit un roulement soumis à un effort F ayant deux composantes, radiale et axiale.
On appelle CHARGE EQUIVALENTE A LA CHARGE F la charge P, purement radiale, qui aurait, relativement à la durée de vie L du roulement, le même effet que l'effort F.
Si l'on trace la fonction P/Fr = f°(Fa/Fr) pour des roulements à billes à contacts radiaux, on obtient la courbe ci contre.
La fonction est égale à 1 pour Fa/Fr=0, décroit tout d'abord quand Fa/Fr augmente, passe par un minimum, puis tend vers une asymptote quand l'effort axial devient prépondérent. Cette diminution signifie que si l'on ajoute une composante axiale modérée à l'effort radial supporté par un roulement, sa durée de vie nominale peut être notablement augmentée, jusqu'à être doublée!. Ceci s'explique par le fait qu'un plus grand nombre d'éléments sont en contact et participent à la transmission de l'effort.
Méthode pratique de calcul de la charge équivalente
La méthode pratique de calcul consiste à remplacer la fonction P/Fr = f°(Fa/Fr) par une fonction majorante F'(Fa/Fr) composée de deux portions de droites.
Dans le cas des roulements radiaux à une rangée d'éléments (fig. 6), on à deux droites d'équations:
- Pour Fa/Fr < e alors P = Fr
- Pour Fa/Fr > e alors P = X.Fr + Y.Fa
|

|
Valeur des coefficients e, X, Y
Elles ont été établies par expérimentations, et sont données dans le catalogue du constructeur de roulement. Elle varient avec la géométrie des roulements.
- X est toujours constant pour un type de roulement donné.
- e, Y sont fonction de l'inclinaison a de l'action de contact au niveau des éléments roulants. Cette inclinaison, constante pour la plupart des types de roulements, peut varier dans un même série:
- suivant les proportions du roulement (c'est la cas des roulements à galets coniques et à rotules sur rouleaux: se reporter alors aux valeurs données dans les catalogues)
- suivant l'intensité de la charge axiale rapportée à une caractéristique du roulement (cas des roulements à billes à gorges profondes)
III-D: Calcul de durée de vie, algorythmes
Choix des roulements rigides à billes
|
Choix des roulements à rotule sur billes ou sur rouleaux et à galets coniques
|
Calcul des montages en "X" ou en "O"
III-E: Passage aux conditions réelles de fonctionnement
Matthieu Barreau (janvier 2001)